摘要:现阶段,电连接器中使用的插孔接触件组合形式大多数为弹性件与刚性件组合。该种组合是通过弹性件与刚性件之间的弹性接触实现插孔接触连接,从而实现电流或信号的传输。就目前国内外常用连接器领域的接触结构情况而言,悬臂式插孔与刚性插针接触结构是连接器领域中应用最为广泛的插孔接触件类型。本文将对该种类型插孔接触件进行概要阐述。
关键词:插孔;插针;连接器
1 引言
电连接器按接触形式可以分为接触式连接器和非接触式连接器,受技术成熟度和使用环境的影响,现阶段,非接触式连接器使用相对较少,接触式连接器仍然是连接器应用领域的主流产品。
无论哪种结构形式的电连接器(接触式),电接触都是其核心功能,而接触件就是实现电接触功能的核心零部件。在国内国外的电连接器领域均有插孔接触件的相关标准,如美军标MIL-C-39029、国军标GJB-1216等,由此可以看出接触件在连接器产品中所占据的地位。接触式电连接器中所使用的接触件大多数为通过弹性件与刚性件之间的弹性接触来实现接触连接功能。就目前国内外常用连接器领域的接触结构情况,悬臂式插孔与刚性插针相组合的接触结构是电连接器领域中应用最广泛的插孔接触件类型。
2 刚性插针
相对于各类型插孔接触件来说,刚性插针从零件结构形式上来说相对比较简单,从加工制造方面来说也相对容易。一般来讲,刚性插针在设计过程中主要考虑使用精度及插针插合的引导端结构即可。通常,为了减小插孔插合力,同时也为了提高插合的可靠性,对插针接触端的表面粗糙度会有较高的要求,插孔接触端的尺寸精度误差一般要求控制在0.03mm范围以内;在插针的插合端应设计成具有直接倒角或锥形倒角的形式,以便于引导插合,如下图所示。

a) 直接倒角图示
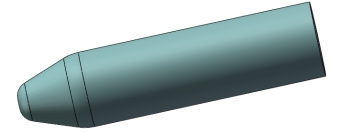
b) 直接倒角图示
图1 刚性插针接触端引导形式图示
需要说明的是,这两种看似微小差异的结构却适用于不同类型的接触件,其中,直接倒角适用于接触端直径在φ2mm以上的插针,而当插针接触端直径小于φ2mm时,一般建议使用锥形倒角。
3 悬臂式插孔
悬臂式插孔主要应用于圆形电连接器中或排列形状比较集中接近于方形的矩形连接器中;该结构适用于22#规格以上的接触件中,不适用于较小的接触件中,从而也不适用于长条形的微矩形连接器中。与刚性插针配合使用,接触寿命可以达到500次以上的水平。
在电连接器的设计中,使用最多的一类插孔就是悬臂式插孔结构,悬臂式插孔又称为集束式多弹性插孔结构,悬臂式插孔结构形式是在圆柱形插孔接触件的接触端开2-8个均匀分布的等分槽。槽的数目视插孔的大小和具体的使用要求而定,开槽后插孔插合端形成和等分槽数目一样多的悬臂簧片,然后再用机械的方法将这些悬臂簧片端部均匀的向中心收口,使其达到规定的接触压力。生产实践中,通常以接触分离力来考核该指标,其结构如下图所示。
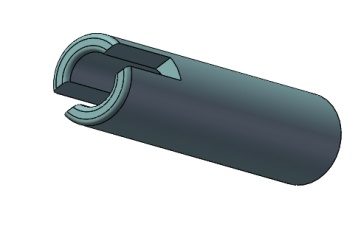
a) 两槽式插孔图示

b) 四槽式插孔图示

c) 多槽式插孔图示
图2 悬臂式插孔图示
两槽和四槽式插孔是低频连接器和射频连接器设计当中,使用最为普遍的结构形式,其插合部位以外的结构形式可根据实际的防转动要求、端接形式来做具体的详细设计。多槽式插孔的典型应用场景相对集中,如导通大电流的接触体、射频同轴连接器的接触体等。多槽式结构具有传输大电流、接触点多、接触可靠等优点。
在设计和使用过程中,为了提高悬臂式插孔的使用可靠性,通常需要在开槽外圆柱面上加装保护套管,即形成闭环插孔,该类保护套管一般由不锈钢薄壁管制成,加装保护套管的作用是在插孔的插合端。保护套管的应用,可防止不相匹配的大直径插孔插针接触件插入;同时,套管的引导孔有利于插针导入插孔,并且有良好的限位功能,可以保证插针不致歪斜,减小插入力,能够对插孔的弹性结构起到保护作用,以防止插孔接触件弹性的失效,从而提高使用可靠性。

图3 加装保护套管的悬臂式插孔图示
4 悬臂式插孔设计计算分析
为便于描述,下面以φlmm插配直径的悬臂式插孔接触件为例进行计算分析。
4.1悬臂式插孔力学模型
对悬臂式结构的插孔接触件进行力学模型分析。其受力情况可简化为悬臂梁,力学模型如下图所示。
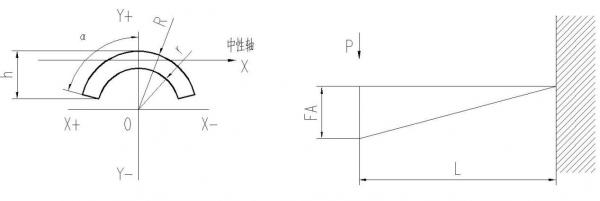
图4 悬臂式结构的插孔接触件力学模型
图中:fA=为插孔接触件簧片挠度,单位为mm;
h为插孔接触件簧片厚度,单位为mm;
L为插孔接触件簧片长度,单位为mm;
取R=0.92mm,r=0.6mm,α=71°,L=7mm,
插孔接触件簧片横截面上最大应力点离中性轴距离
=0.3315(mm)
插孔接触件簧片横截面积
=0.6027(mm2)
插孔接触件簧片质量
=3.75×10-5(kg)
惯性矩
=0.0182(mm4)
4.2悬臂式接触件分离力计算
由于插孔接触件簧片厚度与长度之比h/L≈0.09,因此沿插孔接触件簧片截面的剪应力与正应力相比很小,可以省略不予考虑。最大正应力σmax发生在弯矩插孔最大截面上,即插孔簧片根部。
由式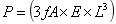

可得插孔接触正压力和簧片正应力计算公式
=0.00784 
=2516.69
该插孔接触件为两簧片式结构,则插孔接触件分离力计算公式为:

式中μ为摩擦系数。
对悬臂式插孔接触件分离力进行理论分析计算:
根据经验,钢质标准针粗糙度Ra为0.8μm,且插孔浸涂保护剂后钢与金之间的摩擦系数μ=0.15;安全系数n取为1.5。根据插孔接触件材料的强度,可以计算出插孔接触件理论允许的最大分离力。
插孔接触件簧片允许的最大正应力 =366.67MPa;
插孔接触件簧片允许的最大挠度 =0.14(mm);
插孔接触件簧片允许的最大接触正压力 =2.78(N);
插孔接触件簧片允许的最大分离力 =0.861(N);
悬臂式插孔接触件满足电性能要求的最小分离力计算:
根据设计经验,对于插配直径为φlmm的悬臂式插孔接触件来讲,接触电阻一般在10~15mΩ之间。满足电性能的镀金接触件的集中电阻最大不会超过为1mΩ,也最多只占接触电阻的10%,所以1mΩ的集中电阻是允许的。
由集中电阻计算式RC=K/Pn(mΩ)
式中K=0.502,n=0.485
则P=0.24N
可得满足电性能要求的最小分离力 =0.072(N)
机械环境要求的插孔接触件分离力计算:
为了确保电连接器在强烈振动、冲击等机械环境下的插孔接触可靠性,必须对强烈振动、冲击等环境条件下插孔接触件需要保证的最小分离力进行计算。
在强烈振动、冲击等机械环境条件下对插孔簧片正压力影响最严重的情况是插针接触件的加速度方向和插孔接触件簧片的加速度方向在某瞬间正好相反,此时要求插孔接触件簧片在承受2倍加速度值的情况下的正压力也必须保证为0.24N。将插孔接触件簧片质量全部集中在簧片端部作为简化的最安全的失效模式,计算如下:
由式
式中 为惯性力,单位为N。
m为插孔接触件质量,m=3.75×10-5kg,
a 为加速度,根据该产品使用要求取a=980m/s2
则此时簧片的极限正压力为
= +0.24=3.75×10-5×2×980+0.24=0.3135(N)
可计算出机械环境条件要求的最小接触件分离力
=0.3 =0.3×0.3135≈0.094(N)
综合考虑插孔接触件理论计算允许的接触件分离力、电性能及机械环境要求的最小接触件分离力,便于生产控制,最后可确定φlmm插配直径的插孔接触件分离力合理数值范围为0.2~1N。
5 制造工艺及注意事项
悬臂式插孔的一般制造工艺为:精密车削加工-铣悬臂槽-其它外形加工-表面处理-簧片收口-插拔力调整-稳定处理-安装保护套管(仅适用于闭式插孔)。加工过程中应注意以下几个方面:
1)车削加工工序中,需要保证加工表面的光洁度要求,对于可取送压接式接触件,要特别注意保证接触件中与卡爪相接触的台阶不能有圆弧过度,以免引起卡爪保持力失效。
2)要保证镀金层厚度要求,接触件的镀金厚度可参照相关国家标准或军用标准,一般情况下,军用产品接触件镀金层厚度应不小于1.27μm,其附着力也必须满足工艺要求。
3)对于压接型接触件,要求尾部进行退火软化处理,以免在接触件与导线压接过程中出现刚性变形和裂纹,影响到压接强度和使用效果。
4)簧片收口需要采用专用的工装,以保证批量生产的一致性。同时,经过收口处理的插孔接触件,需要用标准要求的专用销针进行100%的分离力测试。分离力过小,会造成与插针插合时接触电阻过大,产生超过指标要求的温升,影响信号的正常传输;分离力过大会导致连接器插合过程中插合力过大,不能正常插合,同时影响连接器的正常使用寿命。
5)弹性插孔接触件的材料多选用铜合金。当选用锡磷青铜时,插孔收口预插后,要进行175℃~185℃的稳定处理,以保证簧片弹力的持久性;插孔接触件的材料选用铍青铜时,插孔收口预插后,要进行定型处理(HV320-360),才能充分发挥铍青铜材料的高弹性性能。
6 结语
无论哪种结构形式的电连接器(接触式),电接触都是其核心功能。接触件就是实现电接触功能的核心零部件,而悬臂式插孔与刚性插针的组合应用是电连接器领域的经典组合应用。悬臂式插孔与刚性插针组合,是设计、研发电连接器产品的基础。只有更深入的理解了这类接触件,才能更好的进行电连接器的设计、研发及生产制造工作。 |